BIBO (Bag-In, Bag-Out): Designed with a fully enclosed bag-in and bag-out system, it effectively isolates contamination from radioactive gases, pathogens, and chemicals, preventing secondary air contamination and ensuring the health and safety of personnel.
Features:
Fully enclosed bag-in and bag-out design for a safe and reliable filter replacement process, effectively preventing secondary contamination.
Hermetically sealed: The cabinet adopts full welding technology, with a conventional pressure resistance of ±3kPa. It undergoes an airtightness test at a pressure of ≥2.5kPa before leaving the factory, complying with the standards GB50346-2011 and JG/T497-2016.
Optional Accessories:
PAO scanning device
Differential pressure gauge
Sealing valve
Instrument protection system
Sterilization port, etc.
Primary Applications:
Biopharmaceutical industry (ventilation in workshops for vaccine production, cytotoxins, anticancer formulations, etc.)
Biosafety laboratories (medical research on animal diseases, genetic engineering, etc.)
Radioactive treatment of nuclear fuel in nuclear power stations.
Life Sciences Industry
Air Guard CleanHealth Series Products: Enhancing Safety, Health, and Quality in Livestock Farming
Life Sciences Industry Solution
Improper air handling in biopharmaceutical manufacturing processes poses multiple risks
Pharmaceutical Product Quality: Contaminants such as microorganisms and dust in the air can enter the pharmaceutical manufacturing environment, contaminating pharmaceutical products and leading to their ineffectiveness, side effects, or even posing a life-threatening risk to patients.
Biosafety: Many toxic chemical substances, such as powders and auxiliaries used in biopharmaceutical production, can disperse within the production environment, threatening the cleanliness of pharmaceutical workshops and posing health hazards to employees.
Production Efficiency: Dust and other contaminants in the air can cause corrosion, clogging, and other damage to precision pharmaceutical equipment, resulting in decreased equipment performance and impacting normal operation and production efficiency.
CleanWay Series Air Filtration Products by Air Guard Meet Mandatory Quality and Health & Safety Requirements in the Pharmaceutical Industry
The CleanWay series of air filtration products from Air Guard strictly complies with the mandatory quality requirements of the pharmaceutical industry, effectively removing pollutants such as particles, dust, bacteria, and viruses from the air. It ensures the cleanliness and sterile state of the production environment, thereby guaranteeing the production quality of pharmaceutical products.
It meets the stringent requirements for safety, traceability, and control.
For each area, we have equipped specialized air filters and related equipment to ensure that various needs can be met.
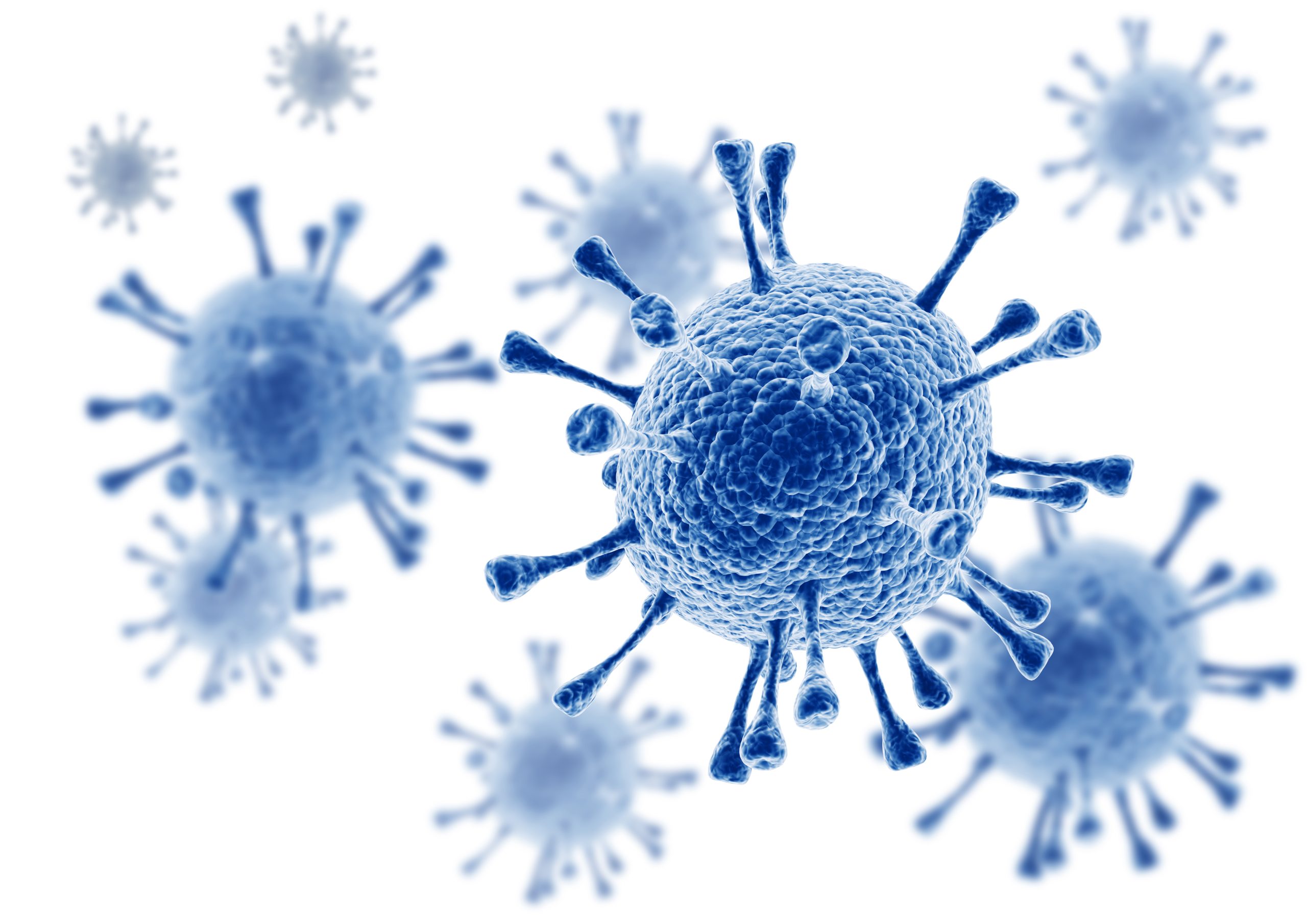
Pharmaceutical Factory Cleanroom Classification | Clean area | Air Guard Purification Filtration Solutions | |||||||||
Grade A | High-Risk Operation Area | Filling areas, areas for placing rubber stoppers and open-necked vial, and aseptic assembly lines. | Maintain the uniform flow environment, stability, and safety of the area through laminar flow equipment to meet rigorous production standards and ensure the quality and safety of pharmaceuticals. | ||||||||
Grade B | Indirectly Affecting Aseptic Operation Area |
Directly surrounding Grade A areas, such as aseptic filling rooms and autoclave cooling rooms. | TC liquid slot filters ensure the cleanliness, stability, and safety of the air within cleanrooms to meet high standards for production or experimental needs, and protect the working environment. | ||||||||
Grade C/D | Transitional Clean Area | Transitional clean areas entering aseptic production areas, such as changing rooms, buffer rooms, corridors, and preparation rooms. | The diffuser outlet HEPA BOX and HEPA FILTER provide high-quality filtered air supply, ensuring employee health and maintaining a clean and safe warehouse environment. | ||||||||
MAU & AHU | Pre-filtration Area for HVAC Systems | Supplies pre-filtered air to various clean areas, as well as the air-conditioning system. | A low-resistance pre-filter with high corrosion resistance, high humidity resistance, and high reliability significantly reduces the operational energy consumption cost of HVAC units, effectively ensures the safety of critical areas, and simultaneously extends the replacement cycle of downstream equipment. |
Air Guard’s Practical Application Solutions and Advantages:
Air Guard has established long-term cooperative relationships with multiple pharmaceutical manufacturing enterprises, focusing on developing products tailored for pharmaceutical process environments.
Compliant with ISO846 standards, we effectively prevent the growth of microorganisms and other contaminants.
Boasting high efficiency and energy-saving features, we minimize operational costs.
With strong stability and corrosion resistance, we can endure the erosion of cleaning and disinfecting agents over a long period without compromising their performance.
Equipped with an intelligent air supply management system, we can automatically adjust to ensure that the terminals always meet the required amount of clean, fresh air on site.
All high-efficiency filter products have completed the EN1822 test before shipment, ensuring compliance with strict standards for safety, traceability, and control.
.png)
Life Sciences Industry Related Productions
BIBO (Bag-In, Bag-Out)
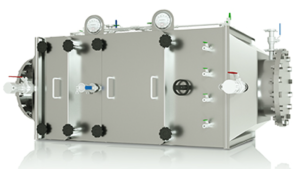
Clean Weighing Hood
Clean Weighing Hood: Provides a high-cleanliness work environment and a leak-free, self-circulating negative pressure clean environment.
Features:
Constructed with a stainless steel cabinet for corrosion resistance and explosion protection, suitable for various complex operating conditions.
Dual-stage negative pressure sealing ensures no leakage.
Modular design allows for customization based on customer requirements.
Control Method:
Touchscreen control enables pressure difference monitoring, fault alarm, and automatic wind speed adjustment.
Routine Testing:
Includes noise measurement, illuminance measurement, wind speed measurement, PAO (Phage Assay of Overall) efficiency testing, downflow airflow uniformity, and electrical safety testing.
Primary Applications:
Used in the biopharmaceutical industry to prevent cross-contamination during the weighing or sampling of pharmaceutical raw materials, ensuring the health and safety of operators.
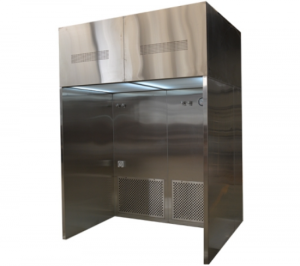
Clean Laminar Flow Hood
Clean Laminar Flow Hood: The vertical unidirectional flow laminar flow hood is an air purification unit that provides a localized Class 100 clean environment, shielding operators and products from cross-contamination.
Features:
Constructed with a stainless steel cabinet and a double-layer negative pressure structure to ensure no leakage.
Modular design allows for flexible installation and can be freely combined according to the available space.
Control Method:
Touchscreen control and centralized control system enable pressure difference monitoring, fault alarm, and automatic wind speed adjustment.
Routine Testing:
Includes airflow pattern testing, noise measurement, illuminance measurement, wind speed measurement, and PAO (Phage Assay of Overall) efficiency testing.
Primary Applications:
Used in production environments and critical equipment in industries such as electronics and semiconductors, biopharmaceuticals, and biological laboratories.
Important process areas such as filling, packaging, and stopping processes.
Shipping and handling of materials and sterile tools and equipment.
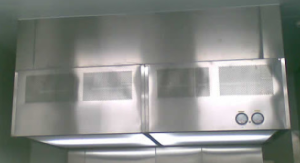
Bio-safe and Efficient Exhaust Vent
Bio-safe and Efficient Exhaust Vent: An efficient filtration unit located in the exhaust section of a cleanroom, equipped with high-efficiency filters and sterilization devices. It effectively isolates harmful gases and dust, preventing environmental contamination.
Features: Made of high-quality stainless steel resistant to acid and alkali corrosion, featuring seamless full welding and excellent airtightness. It can be paired with an in-situ leak detection scanner and a differential pressure gauge to monitor the pressure difference before and after the filter.
In-situ Sterilization: Equipped with a sterilization hood that works in conjunction with the sterilization port in the centralized interface box to perform in-situ sterilization of the interior of the exhaust vent. This facilitates easier and safer operation.
Primary Applications: Utilized in negative-pressure cleanrooms within industries such as pharmaceuticals, food processing, biological laboratories, and hospitals. It serves to filter air in the exhaust section.
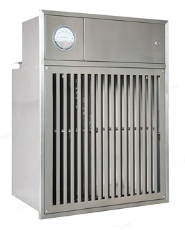
High-Efficiency Air Supply Outlet
High-Efficiency Air Supply Outlet: It is the terminal high-efficiency filtration device of the air supply system in clean rooms, consisting of a plenum chamber, high-efficiency filter, diffuser plate, etc. It can be optionally sealed with a dry gasket or a wet liquid seal.
Features: Robust structure, strong sealing, high versatility, convenient installation and maintenance, capable of PAO testing, etc.
Airflow Adjustment: Stepless upper adjustment valve, internally sealed lower adjustment valve, worm gear adjustment valve.
Diffuser Plate: Mesh, diffusion, swirling airflow around the perimeter.
Main Applications: Used at the terminals of non-unidirectional airflow clean rooms in fields such as life sciences, food and beverage, clean healthcare, microelectronics, etc.
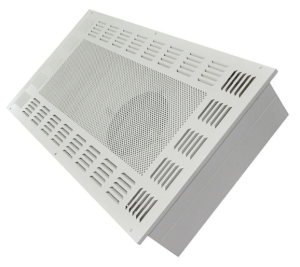
350°C High-Temperature Resistant Filter with Separator
Filtration Grade: H13~H14.
Filter Media: High-temperature glass fiber.
Structure: Separator with ceramic sealing and stainless steel reinforcement.
Continuous Operating Temperature: ≤350°C.
Recommended Final Resistance: ≤700 Pa.
Primary Application: Suitable for high-temperature purification equipment systems such as tunnel sterilization.
Features:
Stable efficiency.
Continuous high-temperature operation.
Particle removal efficiency >99.995% @ MPPS (Most Penetrating Particle Size).
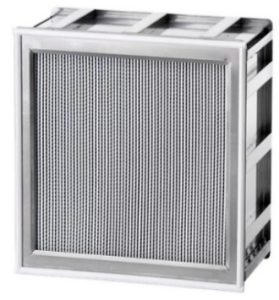
250°C High-Temperature Resistant Filter with Separator
Filtration Grade: H13~H14.
Filter Media: High-temperature resistant glass fiber.
Structure: Stainless steel structure with separator.
Continuous Operating Temperature: ≤260°C.
Recommended Final Resistance: ≤700 Pa.
Primary Application: Suitable for high-temperature purification equipment systems such as high-temperature tunnels.
Features: Low resistance, strong stability, continuous high-temperature operation.
Particle removal efficiency >99.995% @ MPPS (Most Penetrating Particle Size).
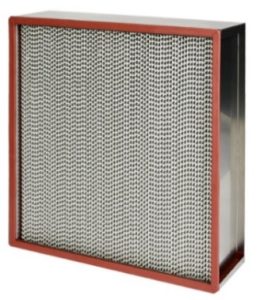
Air Guard CleanWay Box Filter with Separator
Filtration Grade: H13 to H14
Filter Media: Ultra-fine Glass Fiber
Structure: Partitioned Structure with Metal Frame
Continuous Operating Temperature: ≤68°C
Recommended Final Resistance: ≤700Pa
Primary Applications:
Suitable for clean air conditioning systems and high-efficiency air outlets.
Features:
Low resistance and high stability.
Capable of continuous operation at high temperatures.
Particle removal efficiency > 99.995% at MPPS (Most Penetrating Particle Size).
The partitioned structure with a metal frame provides robust support and ensures the filter’s durability and performance in various applications. The ultra-fine glass fiber media offers exceptional filtration efficiency, making it ideal for environments requiring a high degree of cleanliness.
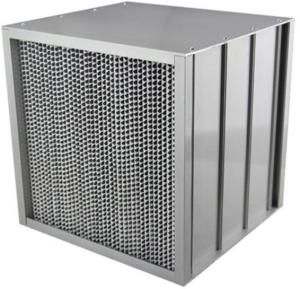
Air Guard CleanWay Non-partitioned Liquid Slot Seal Filter
Filtration Grade: H13 to U15
Filter Media: Ultra-fine Glass Fiber Material
Structure: Wet-Sealed Pleated Panel Design without Separators
Continuous Operating Temperature: ≤68°C
Recommended Final Resistance: ≤350Pa
Primary Applications:
Suitable for the final air supply in cleanrooms of air conditioning systems and clean benches.
Features:
High efficiency with low resistance.
Enhanced liquid slot sealing capability.
Particle removal efficiency > 99.99995% at MPPS (Most Penetrating Particle Size).
The wet-sealed structure ensures a tight seal, further enhancing the filter’s ability to prevent leakage and maintain a high level of cleanliness in the environment where it is used.
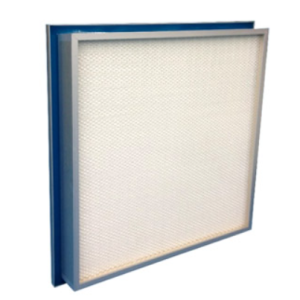
Air Guard CleanWay Panel Filter without Separators
Filtration Grade: E10 to U16
Filter Media: Ultra-fine Glass Fiber Material
Structure: Pleated Panel Design without Separators
Continuous Operating Temperature: ≤68°C
Recommended Final Resistance: ≤350Pa
Primary Applications:
Suitable for the final air supply stage in cleanrooms of air conditioning systems.
Features:
High efficiency with low resistance, ensuring a long service life.
Particle removal efficiency > 99.99995% @ MPPS .
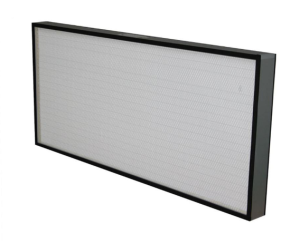